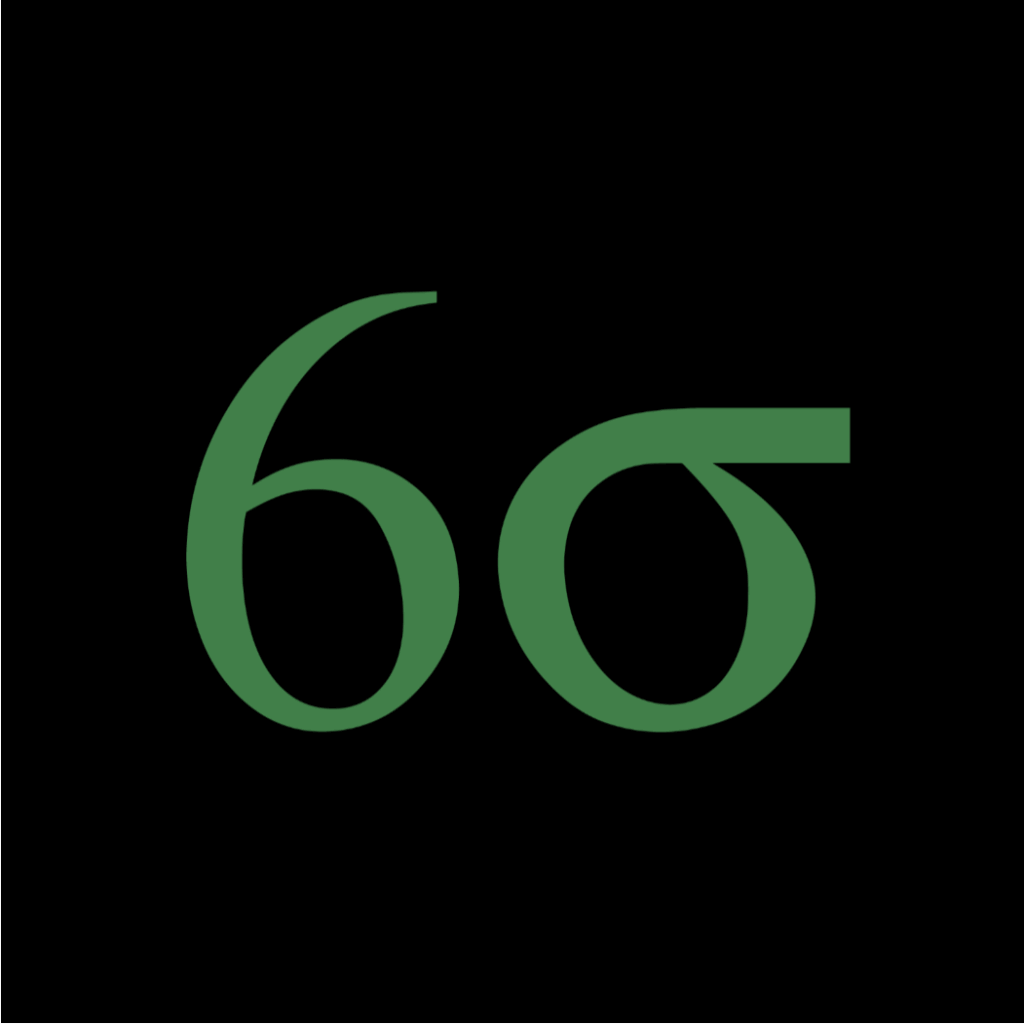
Lean Six Sigma Green Belt
Olympic Steel – Bettendorf, IA and Minneapolis, MN Lean Six Sigma Green Belt Training Team: Joshua Rodriguez, Scott Fuller, Matt Berglund, Melissa Holm, Rachel McCarten, Robert Erion, Will Robbins
In August 2020, Lean Six Sigma Green Belt (LSSGB) training began for five employees in our Bettendorf, IA and Minneapolis, MN divisions. The team of trainees, led by Robert Erion (Safety and Project Manager, and Lean Six Sigma Master Black Belt) and Will Robbins (Process Engineer and Lean Six Sigma Black Belt), each completed a detailed project to earn their LSSGB Certification. This team is taking the lead in making positive, lasting improvements at Olympic Steel.
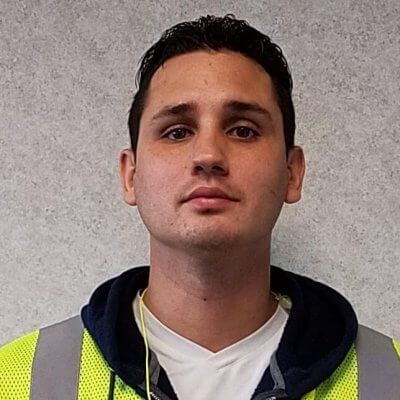
Josh Rodriguez, Quality Assurance Technician, Bettendorf, IA: The new parts/review process was outdated. This caused frustration across multiple departments. Documentation for the part reviews were updated and implemented. Breaks in the process were also identified and corrected by eliminating the reference to people in the process and identifying job functions instead. Additional departments were added to the parts approval process email group to increase communication and collaboration between all necessary departments. Since implementing these changes, productivity and revenue have increased, in addition to the improvements in morale, communication between departments and customer rapport.
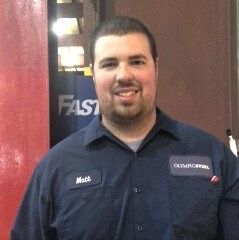
Matt Berglund, Machine Operator, Bettendorf, IA: The material management system, as utilized in the fabrication department, didn’t provide packaging instructions with the work orders. This caused downtime while employees gathered packaging information, and sometimes resulted in incorrectly-packaged goods. Matt used Lean Six Sigma methodology to determine when the customer packaging instructions were entered into the system. Once they learned that instructions were entered correctly, further analysis showed that the instructions did not show up in each step of the process, because the system doesn’t show packaging instructions until the material has been moved through the process to the PKG (packaging) step. To make the instructions available from order entry through shipping, Sales will continue to add packaging instructions when they enter the order in the system, but they will also add the packaging instructions to all steps from order entry through to shipment.
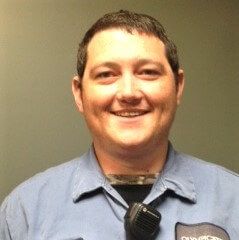
Scott Fuller, Process Engineer, Bettendorf, IA: The Iowa division was challenged to reduce aged inventory by approximately 20% in 6 months. Using Lean Six Sigma methodology, a team comprised of employees from the Scheduling, Sales and Operations Departments established two main areas of improvement, both relating to shipping bays. First, aged material was segregated into a separate area to reduce handling. Second, the areas were scanned to identify all material in the bays. These improvements brought aged inventory down and improved on-time delivery. The segregated material also made it easy to see just how much material is aged.
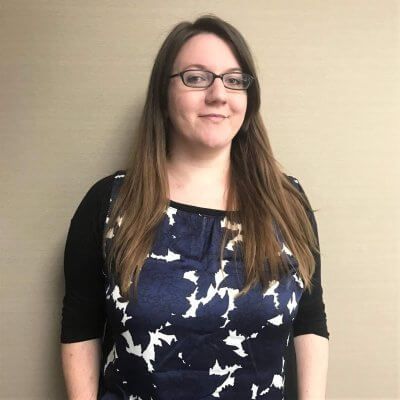
Rachel McCarten, Quality Assurance Engineer, Minneapolis, MN: The Bettendorf, IA division needed help to maintain, update and control their ISO program. Rachel started this project by gathering all ISO documents at the division. Current documents were evaluated by the new process owners and, in some cases, new processes were also created. After review and modification of all old and new processes, files were saved on the Corporate drive (with limited access) and posted as .pdfs files on Olympic Steel’s intranet, OSSIE. This allows for employees to have access to the processes in a controlled state. Maintaining this process will not only secure their ISO certification but will significantly improve quality ratings and continuous improvement efforts throughout each department.
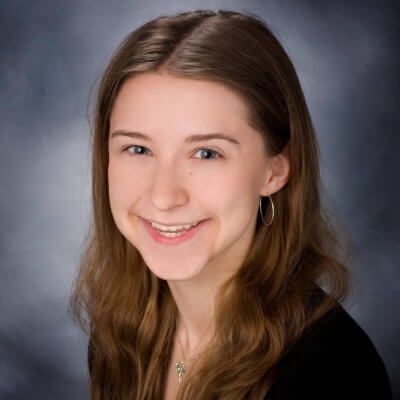
Melissa Holm, Production Planning Supervisor, Minneapolis, MN: The Fabrication Department was challenged to nearly double production without sacrificing schedule accuracy. Melissa used Lean Six Sigma methodology to determine the time spent in each step of the scheduling process and to increase the effectiveness of the existing processes. The analysis of the project identified two main areas of investigation – tag research and status updating. After thorough review and testing of the process at another division, a scheduling tool was developed. There is still work to do to meet the challenge of doubling production, but this project helped establish goals and objectives to help the Iowa division get closer to meeting that challenge. The scheduling tool developed will increase their visibility and allow for more efficient use of time.
Lessons Learned:
This team has learned first-hand that using an established process to identify, assess and resolve issues makes it possible to create and sustain positive changes that can have a big impact locally and across the Company.