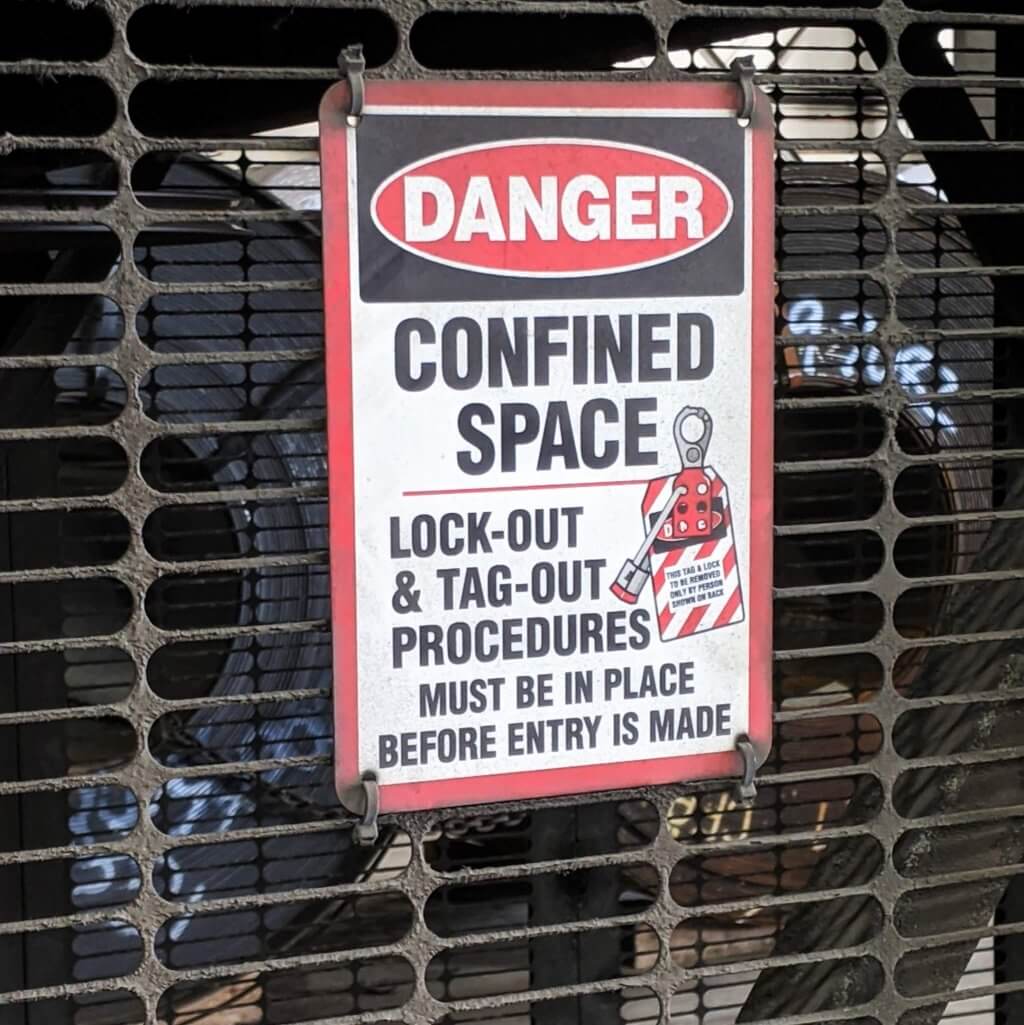
Lock Out / Tag Out and Machine Safeguarding
Lock Out / Tag Out helps keep you safe while equipment is being serviced. It’s one example of machine safeguarding that helps protect us from moving machine parts.
Moving machine parts have the potential to cause severe injuries. Machine safeguards are essential to providing protection from these preventable injuries. Any machine part, function or process that may cause injury must be safeguarded. These safeguards can be divided into three categories: Operational Controls, Physical Controls (or barriers) and Engineering Controls.
Operational Controls are documents we use to train employees how to use the equipment and establish operational constraints – basically, our process. These controls are linear, in a step-by-step process, and completely depend on the employee to maintain a safety focus and execute each step as instructed to maintain operational control. Examples include:
- Standard Operating Procedures (SOPs)
- Work Instructions
- Job Safety Analyses (JSAs)
- Personal Protective Equipment (PPE) Assessments
- Lock-Out/Tag-Out (LOTO) policies and machine-specific LOTO procedures
- Customer specifications or requirements
Physical Controls (Barriers) are guards designed to prevent an employee from interacting with a hazard. When used correctly, physical barriers are a good way to keep our team members safe, but they do not offer operational flexibility. Some requirements for physical barriers/guards include:
- Guards must be in place prior to machine start-up.
- Guards must be durable and protect employees from the hazard.
- Guards cannot allow access from any direction.
- Guards must be installed tool-tight and tool-removable.
- If a guard is not tool-removable, it must be monitored by an electronically monitored safety interlock.
- Damaged or ill-fitting guards must be repaired or replaced.
Engineering Controls are also referred to as Presence Sensing Devices (PSDs). When set up correctly, engineering controls are flexible and allow employees to safely interact with machines or equipment for production needs. Examples include light curtains, safety mats and area laser scanners. Basic requirements for these devices include:
- All PSDs need to be validated prior to the start of operation on each shift.
- Machines designed to operate with PSDs cannot be operated without them (cannot bypass their function).
- The safety distances of all PSDs must be validated annually.
BACK TO BASICS
When performing any kind of work, especially in a manufacturing environment, it’s critical to adhere to Operational Controls, like following procedures. Wearing PPE, referring to work instructions and correctly utilizing the Lock Out/Tag Out (LOTO) process can save a life.
LOTO is a two-part process that isolates energy from the system when a machine or equipment is serviced. Basically, a way to prevent a machine from turning on and potentially harming anyone working on the equipment.
Lock Out physically locks the system in safe mode.
Tag Out is the labelling process used to identify why the LOTO is required.
LOTO procedures are important because they keep you safe!
Safety devices such as barrier guards or guarding devices (barrier controls) are installed on systems to maintain user safety while these systems are being operated. When non-routine activities take place, like maintenance or other service to the equipment, these safety devices are removed. This poses an increased risk of injury, and LOTO helps decrease that risk.
QUESTIONS?
If you have any questions about machine safeguarding or LOTO, please reach out to your local Safety leader or Tony Dominic, Vice President – Safety, Health and Environment, at Tony.Dominic@olysteel.com.
Safety First. Always. And, it starts with me.